[Herald Interview] Group14, SK Materials to operate Asia’s largest silicon plant for EVs
Sangju plant to produce silicon battery materials enough for 100,000-200,000 EVs next year
By Byun Hye-jinPublished : Dec. 17, 2023 - 14:56
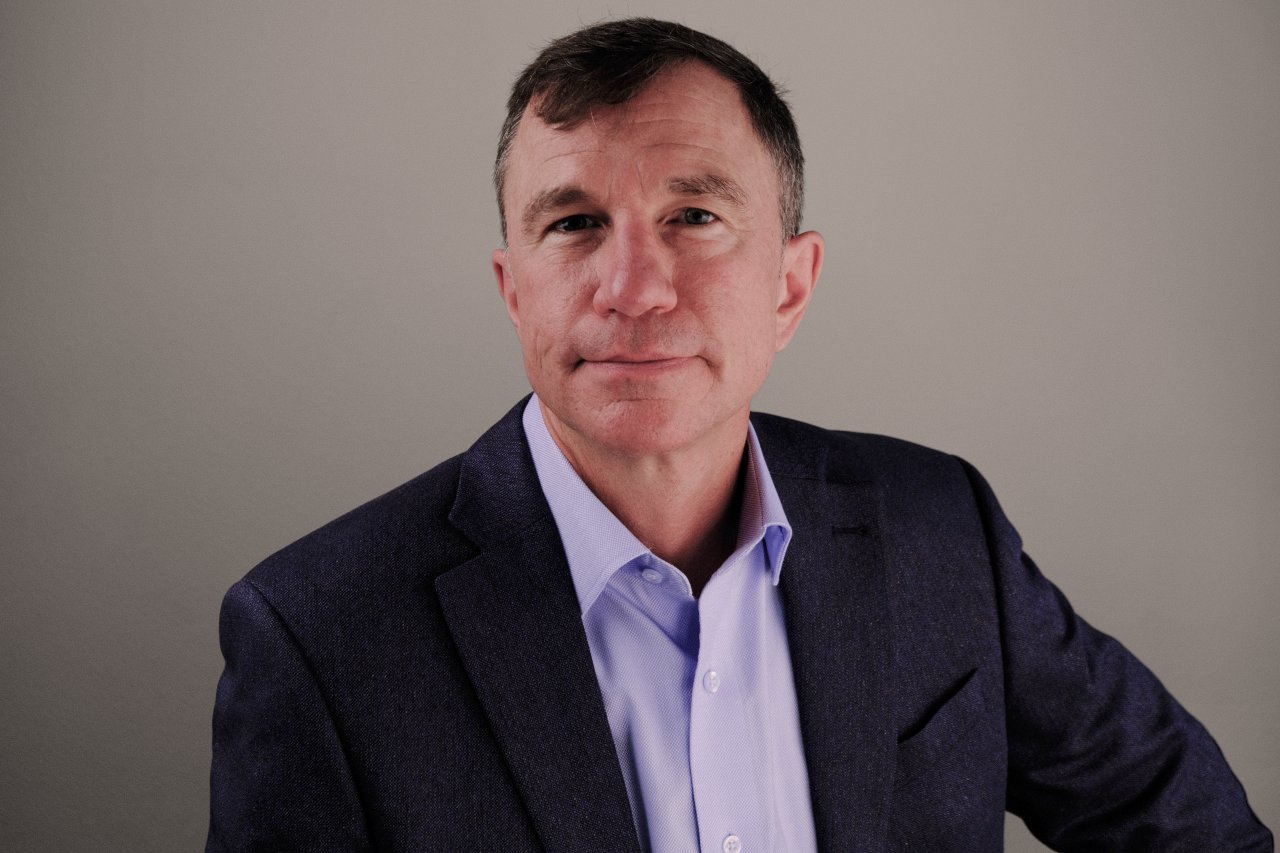
The joint venture between Washington-based Group14 Technologies and SK Materials, a chemical materials unit under Korea’s SK Group, will start the commercial operation of Asia’s first large-scale manufacturing plant for silicon battery materials in Sangju, North Gyeongsang Province, early next year.
“(SK Materials Group14), the joint venture in Sangju, is the Asia’s first electric vehicle-scale silicon anode manufacturing facility that will go online very soon in the next month or so,” Group14 Technologies CEO Rick Luebbe told The Korea Herald in a recent interview.
Using a modular system, which standardizes the manufacturing process with high efficiency, the plant will start production of Group14’s flagship active silicon battery material, called SCC55, with an initial annual capacity of 2,000 metric tons -- equivalent to 10 gigawatt-hours of battery capacity and enough for 100,000 to 200,000 units of electric cars.
The Sangju plant signifies the importance of the partnership with SK, leading up to the launch of Group14’s second fully-owned commercial factory in Moses Lake, Washington next year.
Emphasizing the significance of dual sourcing for the introduction of new technologies, Luebbe said that the automotive industry can’t simply base a platform on a technology that can only be accessed from one potential supplier.
“We’ve sought out the best partner to enable an independent second source for those automotive customers, and we picked SK because of their leadership in batteries,” he said.
The battery industry is showing strong interest in pushing forward the technological transition from graphite-based lithium-ion batteries to using more advanced anode materials like silicon, according to the CEO.
Compared to graphite, the silicon-carbon composite SCC55 can increase a battery’s energy density up to 50 percent, which significantly reduces the cost at the battery pack level.
“This material is less expensive on a dollar per kilowatt-hour basis at the pack level (than graphite lithium-ion batteries),” Luebbe said. “Due to its high energy density, we can take a third of the battery cells out of the path and still have the same (driving) range. This results in significant cost savings -- lower cost of EVs.”
Luebbe also noted that SCC55 batteries enable “extreme fast charging” of five to 10 minutes, similar to charging internal combustion engine cars. Currently, it takes around 20 to 50 minutes to charge electric cars installed with lithium-ion batteries.
With dozens of global companies working on silicon batteries, Luebbe said that Group14 has the advantage of being years ahead of other players. Aside from the first EV-scale production facility, its battery products are already sold commercially in cell phones in China.
Recognizing the strategic importance of the Korean market, a key battery powerhouse, Luebbe pointed out that three of the five largest battery manufacturers in the world are Korean firms -- LG Energy Solution, Samsung SDI and SK On.
“So we secured further intellectual property protection -- that is, patents -- for our technology, products and manufacturing processes here,” he said.
“We don’t currently envision other joint ventures in Korea. However, we will certainly be happy to partner with both strategic partners and customers with SK On as well as LG and Samsung to help grow the overall industry.”
The recent supply glitch issue on graphite mined from China gives a further push for Korean battery makers -- who have been highly dependent on these raw materials -- to replace them with silicon, Luebbe added.